In Warffum, Groningen, Aviko Rixona processes potatoes into dried potato granules. Cooking, processing and drying food is a technological process that consumes a lot of energy. To reduce the factory’s energy consumption, and thus its CO2 emissions, Aviko Rixona in Warffum has installed the first heat pump within Cosun. Jeroen Zwietering is Energy Process Engineer at Aviko Rixona and is working on realising the energy transition of three plants within the company. We spoke to Jeroen about the heat pump project in Warffum, a project with which he has been involved since the conception of the idea through to its implementation.
Connecting processes
As part of the approach within the SCO2RE+ programme, Jeroen and his team began analysing the production lines in the factory. “We identified an opportunity to combine two processes in Warffum that require a lot of energy: a heating step and a cooling step. It was possible to connect the two processes using a heat pump,” Jeroen explains. In the next step, they analysed heat pump capabilities and the potential business case. Jeroen: “It has to make sense in terms of cost, energy savings and revenue. In addition, it mustn’t interfere with operations. The factory has to be able to keep running, the operators have to be able to work with the new solution, and it must be safe.”
Long delivery times
The project was launched in 2020, in the midst of the Covid pandemic. “Despite restrictions and long delivery times for materials, the project proceeded efficiently,” Jeroen explains. “The heat pump was completely assembled on site at the manufacturer’s premises. Our colleagues made all the preparations in our factory, such as piping and other adjustments to the building.” Once the machine was finished, it was transported to Warffum on a flatbed trailer. Within 1-2 weeks, the heat pump was installed and operational. “It was challenging, but everything went smoothly and worked out as planned. This is thanks to the commitment and cooperation of all our colleagues who worked on the project.”
550 households
The heat pump in Warffum uses residual heat from cooling water to heat water in another process step. “We’re winning with the heat pump in two areas: lower consumption of natural gas for heating and less electricity for cooling. With this new system, we’ve achieved a reduction in gas consumption equivalent to around 550 households. And it’s actually using a technique that has been known for years from refrigeration technology, just like your fridge at home. Only now, we apply the design to the heating and not the cooling function. And that’s actually the crux of the system, that you start thinking differently.”
Proven technique
Jeroen sees this project as a blueprint for increasing the sustainability of other production lines within Aviko Rixona: “With this heat pump, we’ve proven that the technology works and that relatively few adjustments are needed within the operation to achieve substantial energy gains. Wherever there’s a combination of hot and cold flows within a process, a heat pump could make a difference. Within Aviko Rixona, I can easily come up with several potential areas.”
Combination of steps
“To make real strides in reducing energy consumption, you have to involve everyone in the organisation,” Jeroen believes. “It’s a combination of big steps, like a heat pump, and small steps, such as looking at indirect issues. Energy loss is one such issue. It’s important that everyone is aware of where energy is being consumed and lost within their area of expertise. If you use a lot of cleaning water, it takes extra energy at the water treatment plant. If your whole operation is running, but you’re losing potatoes, that also means you’re wasting energy. It all starts with thinking differently and becoming more aware of what can be done. There are huge gains to be made if everyone is clear about the effect their actions have on energy consumption.”
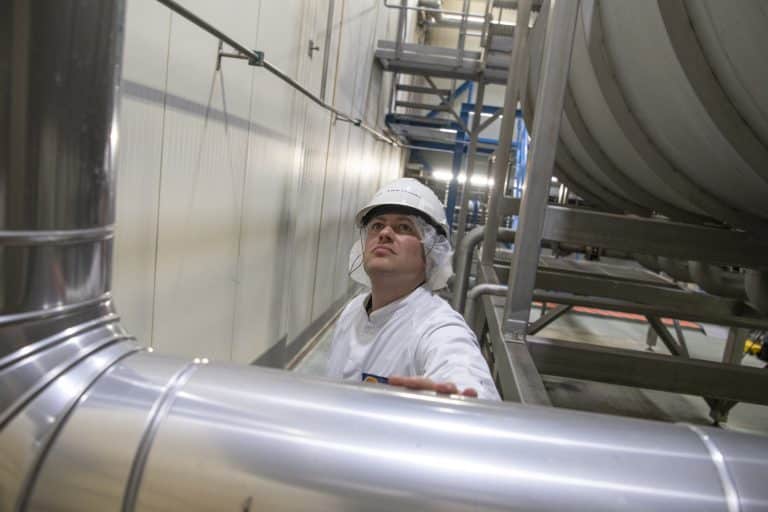